From part design to finished piece, IHTS offers proven technologies that reduce material costs, improve part strength and eliminate post-heat treatment remediation costs.
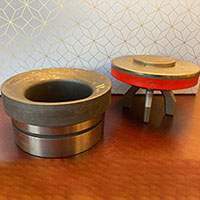
Dual Austenitizing Temperature (DAT®)
IHTS’s patent pending DAT® (“Dual Austenitize Temperature”) staged heating methods applies uniform heating to every profile of the part, whether it is symmetrical or not, so the entire surface attains the same austenitizing temperature necessary to allow the subsequent high-pressure intensive quench (HPIQ®) process to instantly set the part’s metallurgical "shell" to create beneficial residual compressive surface stresses, which aids to eliminate part cracking.
Learn more.High-Pressure Intensive Quench (HPIQ®)
Since the late 1990s, experiments in high-pressure intensive quenching revealed the misconceptions of established heating and cooling methodologies which asserted that gradual cooling resulted in optimum part quality while reducing distortion.
Learn more.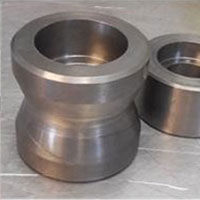
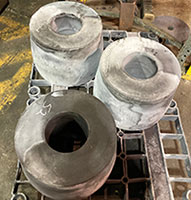
Direct from the Forge Instant-Impact Quenching (DFIQ™)
By quenching parts direct from the forge, the Instant-Impact Quenching unit eliminates the energy waste of cooling in air and having to austenitize again before quenching. Very high intensity quenchant flow is needed at the part surface shell to eliminate non-uniform film boiling and prevent the part from cracking.
Learn more.Instantly Quenched Ductile Iron (IDQI®)
IHTS’s patent pending Dual Austenitizing Temperature (DAT®) Heating process combined with our High Pressure Instant-Impact Quenching process can enable part makers to switch from case carburized steel parts, eliminate long, batch case carburizing furnace cycles and use a low cost, readily available ductile iron cast material and heat treat the part in a single-part flow.
Learn more.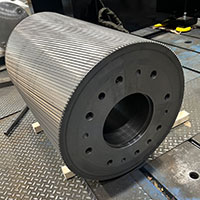